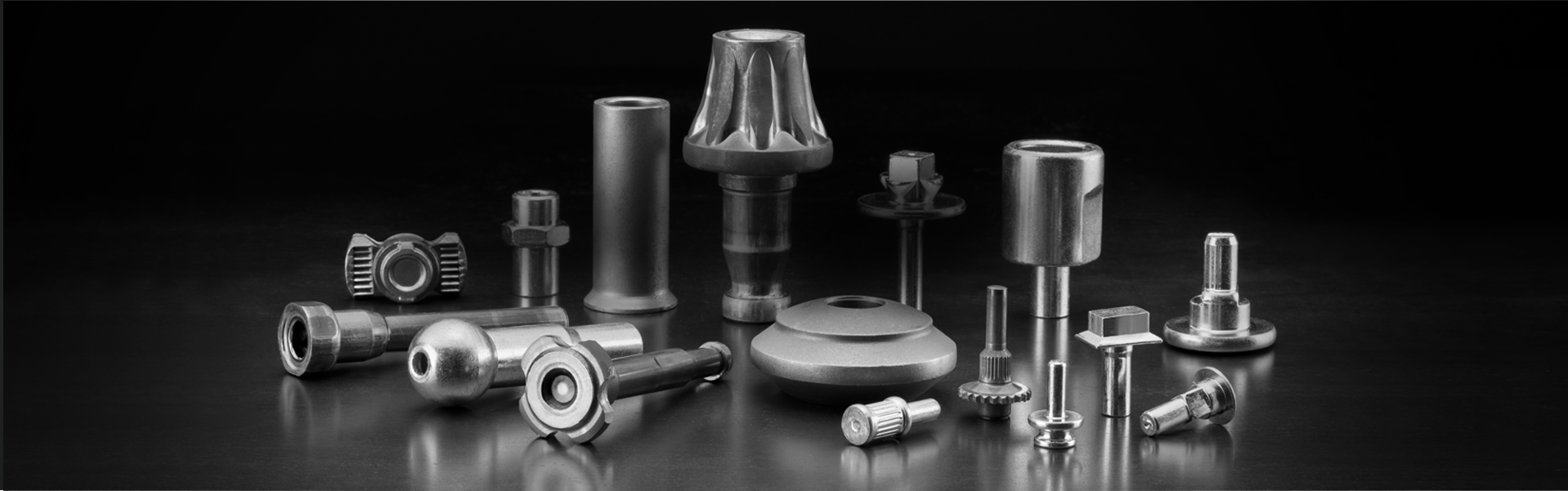
Conformación en Frío
La conformación en frío es una tecnología con una gran tradición, que continuamente está reinventándose y sobrepasando nuevos límites. TEMSA cuenta con más de 30 años de experiencia en el diseño y fabricación de herramientas para proyectos multiestación. Desde rótulas, tornillos y tuercas especiales, engranajes, elementos de fijación especiales, laminación de tubo, extrusión de aluminio, balística… el rango de productos es muy grande.
TEMSA está presente en la mayor parte de procesos por conformación en frío del mercado.
Desde la fabricación de series grandes a unidades sueltas, TEMSA cuenta con la tecnología necesaria para ayudar a cada cliente en aquello que necesita.
TEMSA tiene gran experiencia en piezas con grandes cambios de sección o con solicitaciones importantes durante la fabricación. En especial en piezas que requieran de extrusiones importantes o fabricación de herramienta modular, o donde la utilización de tecnología, como las matrices abiertas, represente una barrera de entrada importante para los fabricantes. Allí donde haya un problema que requiera una solución es donde estará presente TEMSA.
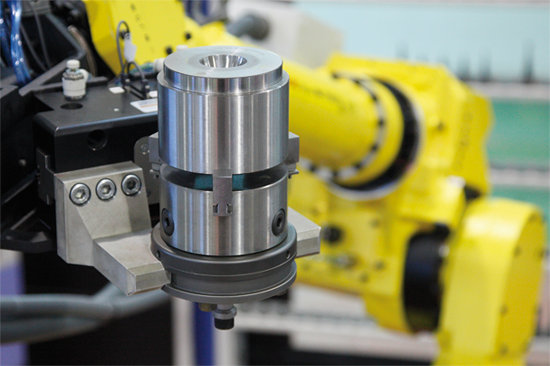
La conformación en frío
La conformación en frío es un proceso de deformación metálica en el que alambre es cortado a una longitud determinada y deformado a temperatura ambiente mediante su inserción en matrices de acero o metal duro dispuestas en 2 o más estaciones consecutivamente.
Este proceso se lleva a cabo aplicando presiones muy elevadas que deforman el material más allá de su límite elástico pero sin llegar a su punto de rotura. De esta manera se pueden conseguir piezas de alta complejidad sin apenas pérdida de material y a una velocidad muy elevada, produciendo series largas de piezas idénticas con unos costes muy reducidos.
Hay una serie de operaciones básicas en las que se basan todos los procesos de conformación en frío. Las principales son cizallar, reducir, recalcar, extrusionar, perforar, recortar y bruñir. Existe un tipo de herramienta para cada operación, con una geometría, material y recubrimiento específico adaptado a lo que se quiere conseguir.
LA TECNOLOGÍA
La tecnología ha avanzado mucho los últimos años, y lo que antes era imposible ahora es normal. Cada límite se supera a diario. A ello han contribuido varios factores, que combinados hacen que el sector se reinvente constantemente:
Mejoras en los materiales: El metal duro evoluciona constantemente y los sinterizadores de esta materia prima no paran de sacar al mercado calidades específicas para cada tipo de proceso. Donde antes se requería Widia, ahora se describe exactamente la composición, el tamaño del grano y las propiedades necesarias. Con esto se ha conseguido mejorar enormemente los rendimientos de las herramientas. Y por otro lado los aceros cada vez son más específicos, con una variedad importante de tipologías, desde aceros rápidos, pulvimetalúrgicos, con diferentes tratamientos supletorios, etc, que pueden llegar a competir con el metal duro en cuanto a prestaciones.
Mejoras en la maquinaria utilizada: los productores de herramientas utilizan maquinaria cada vez más precisa y que trata mejor las superficies. Máquinas CNC con superacabados, que evitan microfisuras, que dejan un Ra que hace unos pocos años era imposible ni tan siquiera imaginar. Además, las prensas de la conformación en frío son cada vez mejores, más rápidas y con mejores controles.
Soluciones constructivas: la simulación es un gran aliado en la conformación en frío, pero es la imaginación y el saber hacer de los técnicos el que propone soluciones que ahorran costes y mejoran rendimientos o incluso quien hace posible fabricar por conformación piezas que parecía que solo podían ser torneadas. Así, la intercambiabilidad de núcleos, la aplicación de recubrimientos en zonas específicas, las mejoras de diseño y las pruebas sin fin consiguen llegar a donde antes no se llegaba.
EL ACABADO
Las tolerancias tienen que ser acordes con el producto a conseguir, pudiendo llegar hasta los +/- 0.005. El material a utilizar podrá ser de metal duro o acero, pudiendo utilizar todas las calidades de metal duro y todos los tipos de acero – especiales, rápidos, pulvometalúrgicos, etc.- para aprovechar las cualidades más adaptadas al proceso al que van destinadas y que tengan una mejor funcionalidad. Junto al material y la forma, son de vital importancia los acabados superficiales –en el rango de Ra0.5- que influirán decisivamente en la vida útil de la herramienta.
LOS RECUBRIMIENTOS
Posteriormente se pueden mejorar las cualidades de la herramienta mediante la aplicación de un recubrimiento, en sus diferentes modalidades. Cada recubrimiento –TiN, TiAlN, AlCrN, DLC, entre otros- aportará unas cualidades específicas supletorias a la herramienta. TEMSA trabaja con a las mejores empresas del mercado de aplicación de recubrimientos para ofrecer a sus clientes las mejores opciones para aumentar sus prestaciones.
MATERIAL DE RECUBRIMIENTO | MÉTODO APLICACIÓN | GROSOR DE CAPA | COLOR | CAMPO DE APLICACIÓN |
---|---|---|---|---|
AlCrN | PVD | 2-6mm | Gris metálico | Alta resistencia a la oxidación. Procesos de punzonado y corte en conformación y corte fino. |
TiN | PVD | 2-4mm | Dorado | El recubrimiento más usual para cualquier aplicación : prensado, punzonado, reducción y recalcado. |
TiCN | PVD | 2-4mm | Plateado claro | Un recubrmiento superior al TiN, cuando se necesita una mayor protección al desgaste por abrasión. Reducción de la fricción cuando los elementos rozan entre ellos al moverse. |
CrTiN | PVD | 6-12mm | Plateado claro | Para algunas aplicaciones al trabajar con acero inoxidable. |
TiAlN | PVD | 3-12mm | Gris-violeta | Cuando se genera alta presión y calentamiento y las rebabas pueden ser un problema. |
DLC | PVD | 1-3mm | Negro | Diamond-like-coating o recubrimiento-como-el-diamante. En aplicaciones con aluminio –recalcado, extrusión- previene la abrasion y la adherencia del aluminio a la capa superficial de la herramienta. |
CrN | PVD | 2-4mm | Plateado claro | Para cuando se reducer el índice de fricción con otros materiales. Tiene una ductilidad y grosor mayor que otros recubrimientos. Aumenta el punto de fatiga y la resistencia al escarbotamiento y rotura, como también al de corrosión y oxidación |
WC/C | PVD | 2-5mm | Negro carbón | Para reducir la adherecia de materiales. Existe la posibilidad de añadirlo posteriormente a otros recubrimientos por métodos dúplex para así mejorarlos, como AlCrN. |
TiC or Tin/TiC | CVD | 7-9mm | Gris metálico o dorado | Chemical Vapor deposition o Deposición química al vapor (frente a Deposición física al vapor o PVD). Consigue una resistencia extrema al desgaste por abrasión e impacto, mejora enormemente la resistencia a la adhesión y baja la temperatura de fricción. |
METAL DURO
TEMSA ha desarrollado y fabrica herramientas específicas para las aplicaciones de desgaste y corte en diferentes calidades de carburo de tungsteno o metal duro.
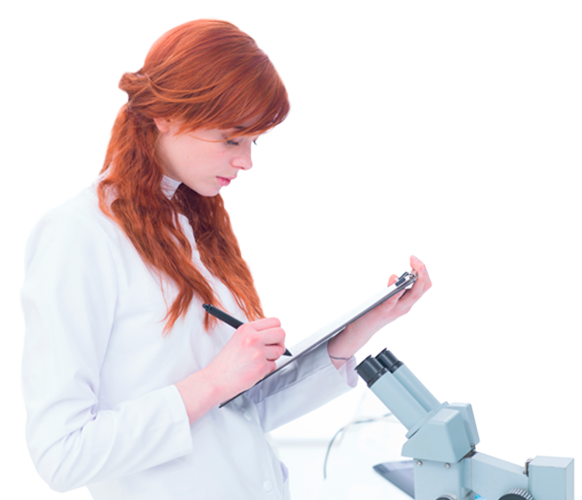