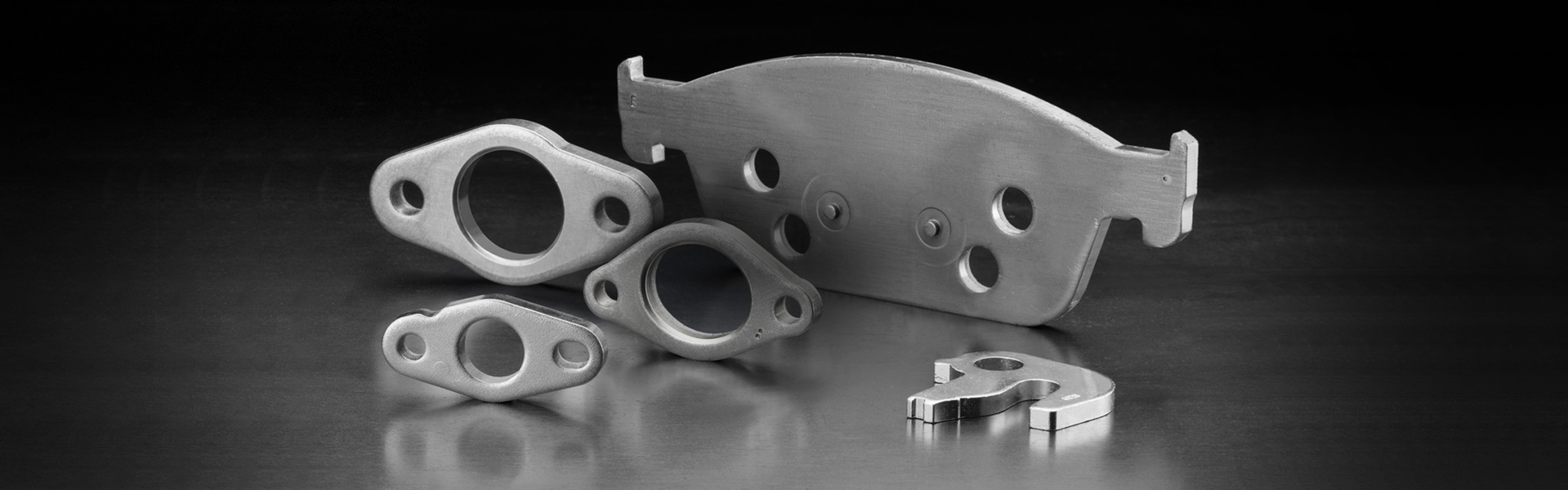
Fine blanking
TEMSA supplies the blank punches and guide and die plates to the leading manufacturers of parts produced by fine blanking in the industry. From locks to automotive parts, this is a growing market for TEMSA.
The processes in the manufacturing of tools for fine blanking are very different if we’re talking about blank punches and guide and die plates. The carbide blank punches have a much longer lifespan and retain a better surface finish than steel blank punches and because of this processes and machinery are needed to ensure that there’s a perfect concentration the entire length of the punch. TEMSA has two Rollomatic grinding machines working in an especial way of grinding called peeling process, and in only one workload the entire outline is obtained, cylindrical or convex.
On the other hand, the blank punches have an asymmetrical shape that can’t be obtained by conventional methods and require the application of the wire EDM process and high speed machining.

INTRODUCTION
Fine blanking is an extremely precise metal deformation process which is a mix between stamping and cold extrusion but there’s a clear difference between them both because of the presses used and because of the specific machines needed as well as the product obtained.
The advantages of using fine blanking over the other processes are, amongst others, the range of products that can be obtained, now that the thickness of the sheet punched is up to 19mm. Even with such thick material, the cut finishing is of top quality, without burrs, with an excellent level of flatness, and straight edges.
Additionally, it’s possible to obtain very small orifices in comparison with the thickness of the sheet. A very important factor is that in addition to production series the parts should have perfect repeatability, consequently this assures that the part will be the same regardless of when it was manufactured.
The guide and die plate and the blank punch must have a narrow clearance of 0.5% or less so that the tolerances are within 0.001mm. Furthermore the surface finishes must be excellent, with a roughness of less than Ra 0.5 in order to allow the blank punch to slide through the guide and die plate and perforate or cut the sheet plate properly also needing to avoid wear due to friction and increasing its lifespan.
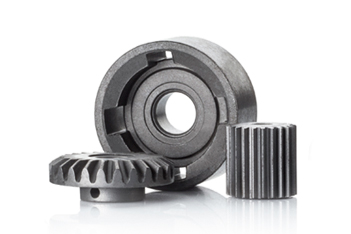
POWDER METALLURGY
The company supplies tools to all of the large groups that manufacture sintered parts.
CARBIDE
TEMSA has developed and manufactured tools specifically for wear and cutting applications in different grades of tungsten carbide.
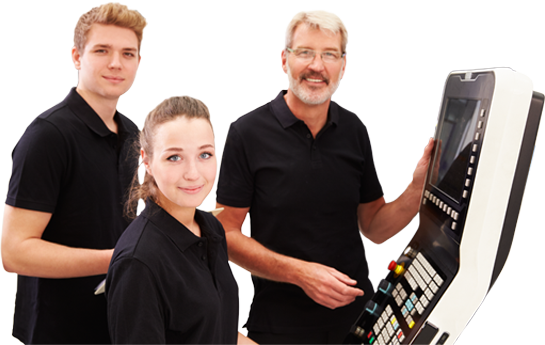